The Importance of Welding WPS: Ensuring Quality and Safety in Your Projects
The Importance of Welding WPS: Ensuring Quality and Safety in Your Projects
Blog Article
The Ultimate Guide to Welding WPS Procedures: A Thorough Introduction for Welders
In the detailed world of welding, Welding Treatment Requirements (WPS) offer as the foundation of ensuring quality, consistency, and safety and security in welding procedures (welding WPS). As we delve into the numerous parts of a WPS and discover the intricacies of credentials and accreditation, we will certainly uncover the important duty these treatments play in the world of welding.
Relevance of WPS Procedures
Recognizing the importance of Welding Procedure Specifications (WPS) procedures is crucial for guaranteeing the high quality and integrity of bonded frameworks. WPS treatments function as a roadmap for welders, laying out the required steps, specifications, and products needed to accomplish an audio weld. By sticking to WPS standards, welders can ensure consistency in their job, leading to structurally sound and dependable welds.
One of the primary factors why WPS procedures are vital is their duty in keeping weld quality and integrity. Following the specified welding parameters and strategies described in the WPS helps prevent problems such as porosity, splitting, or insufficient combination, which can jeopardize the toughness and sturdiness of the weld.
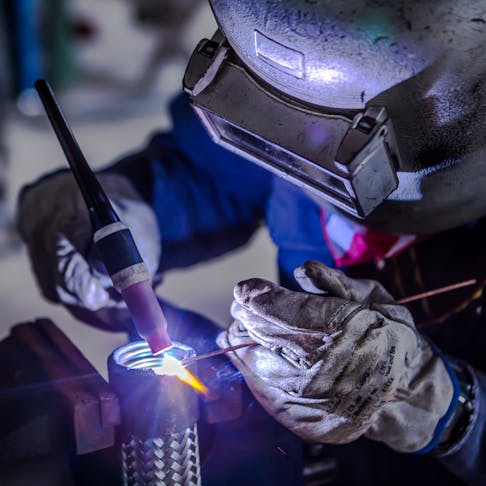
Components of a WPS
A Welding Procedure Specification (WPS) normally consists of important components that information the details needs for performing a weld, ensuring uniformity and quality in the welding procedure. The crucial elements of a WPS consist of necessary variables such as base metals, filler steels, interpass and preheat temperatures, welding procedures, shielding gases, welding positions, and post-weld warmth therapy demands.
Base steels refer to the materials being signed up with, while filler steels are utilized to load the void in between the base steels during welding. The welding procedure lays out the particular strategy to be utilized, whether it's gas steel arc welding (GMAW), protected steel arc welding (SMAW), or an additional method. Welding positions define the positionings in which welding can be performed.

Certification and Certification
Having established the important components of a Welding Treatment Specification (WPS), the emphasis now shifts towards the essential elements of certification and certification in welding techniques.

Accreditation, on the various other hand, is the formal recognition of a welder's certifications by a relevant qualification body or company. Welding accreditations are commonly based upon the specific welding processes, products, and settings a welder is certified to deal with. Holding a valid welding accreditation demonstrates that a welder fulfills industry criteria and is skilled to carry out welding tasks to the needed requirements.
Creating a WPS
To develop a Welding Procedure Requirements (WPS) that fulfills sector read this post here criteria, mindful factor to consider of welding processes, materials, and operational specifications is crucial. The first action in creating a WPS is to recognize the welding process to be utilized, such as gas steel arc welding (GMAW) or protected metal arc welding (SMAW)
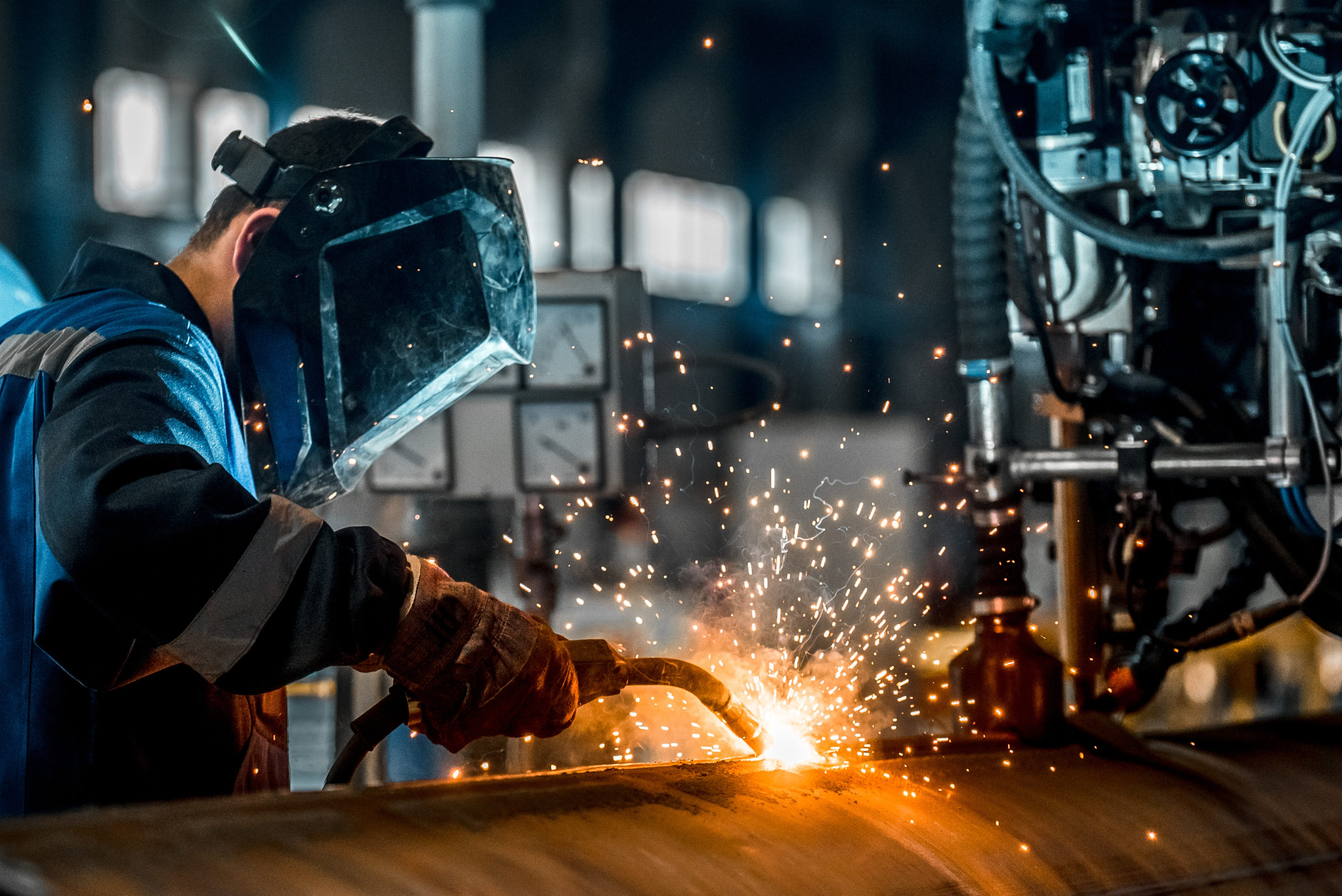
Carrying Out and Monitoring WPS
Upon wrapping up the extensive Welding Treatment Specification (WPS) that diligently details welding processes, products, functional specifications, and quality guarantee steps, the emphasis shifts to efficiently carrying out and keeping track of the established treatments. Application entails making sure that all welders involved in the job are familiar with the WPS and follow it diligently during the welding procedure. Efficient implementation and tracking of the WPS are critical for ensuring the integrity, strength, and safety and security of the bonded joints, ultimately helpful site adding to the total success of the welding task.
Verdict
In conclusion, understanding and adhering to Welding Procedure Specifications (WPS) is important for welders to guarantee top quality, consistency, and security in their job. By knowing the elements of a WPS, getting proper qualifications and accreditations, developing thorough treatments, and executing and monitoring them properly, welders can improve their skills and efficiency in welding techniques. Complying with WPS treatments is crucial for creating high-quality welds and meeting market requirements.
In the complex world of welding, Welding Procedure Requirements (WPS) offer as the backbone of making sure quality, consistency, and security in welding operations. The welding procedure describes the certain technique to be made use of, whether it's gas steel arc welding (GMAW), protected metal arc welding (SMAW), or an additional method.To establish a Welding Treatment Specification (WPS) that satisfies market requirements, cautious factor to consider of welding processes, products, and operational specifications is necessary. The initial action in creating a WPS is to identify the welding process to be utilized, such as gas metal arc welding (GMAW) or secured metal arc welding (SMAW)Upon wrapping up the detailed Welding Procedure Specification (WPS) that thoroughly details welding processes, materials, functional parameters, and top quality assurance steps, the focus moves to properly executing and keeping track of the recognized procedures.
Report this page